1.What does a car heat exchanger do?
The automobile heat exchanger mainly takes the heat away through the cooling medium through energy conversion. Common cooling media are coolant, refrigerant, and air. For example, engine radiator on a car takes away heat through coolant, the condenser takes away heat through refrigerant (such as R134a, R1234yf or carbon dioxide R774) through vapor-liquid two-phase evaporative condensation.
Keys take away:For a Coolant loop power dissipation 25 kW you will need Qm 1 kg/s. For a Refrigerant loop power dissipation of 5 kW, need only Qm 0.04 kg/s. 5 times higher the power dissipation, but 25 times higher in coolant flow rate, do you know why?
2.Heat and mass transfer
Heat and mass transfer are very important for car heat exchanger, heat exchangers design based on heat and mass transfer. We need to understand physical laws driving the phenomena of heat and mass transfer.
Hence the heat transfer modes(convention and conduction), pressure drop, heat transfer are important for car heat exchangers.
Latent heat:
ΔQ enthalpy stored or exchanged during heat transfer with phase change.
ΔQ = M . L (Joule)
Here, M is the mass(kg), L is specific latent heat (J/kg) depending on temperature and pressure conditions.
Table of fluid thermodynamic properties
Liquid state | T_evaporation(℃) | Pressure(bar) | L(J/kg) evaporation |
water | 100 | 1 | 2260,000 |
Ethylene Glycol | 198 | 1 | 800,000 |
R134a | 0 | 2.9 | 198,000 |
R134a | 60 | 16.8 | 139,000 |
R1234yf | 0 | 3.1 | 168,000 |
R1234yf | 60 | 16.4 | 112,000 |
CO2 | 0 | 32 | 242,000 |
See above table, if your car store 0.8Kg R1234yf refrigerant in the AC loop , then it could absorb 0.8×168,000=134.4kj heat to evaporation at T of 0℃.
Sensible heat:
ΔQ enthalpy stored or exchanged during heat transfer with temperature variation.
ΔQ = M . Cp . ΔT (Joule)
Here, Cp is the Specific heat (J/kg.°C).
Table of material density and specific heat capacity
Metal | ρ(kg/m3) | Cp(J/kg.K) |
Aluminum | 2700 | 900 |
Copper | 8950 | 385 |
Inox | 7800 | 460 |
Liquid | ρ(kg/m3) | Cp(J/kg.K) |
Ethylene Glycol | 1097 | 2360 |
R134a (liq. saturate 0°C) | 1293 | 1350 |
R134a (liq. saturate 60°C) | 1052 | 1680 |
gas | ρ(kg/m3) | Cp(J/kg.K) |
R134a (vap. saturate 0°C) | 14.4 | 920 |
R134a (vap. saturate 60°C) | 87.1 | 1400 |
air | 1.2 | 1000(1bar at 20°C) |
The product of ρ and Cp is known as the volumetric heat capacity, examples of aluminum volumetric heat capacity is 2700×900=2.5MJ/m3.k, volumetric heat capacity for Ethylene Glycol is the same as aluminum ,while the air is much smaller volumetric heat capacity of 1.2KJ/m3.k.
Keys take away: Heat transport capacity is limited for gas.
Keys take away: CO2 has interesting thermodynamic properties compared to R134a and R1234yf but difficult to use (considering pressure, safety), much high operation pressure, high burst pressure for horse, tube and heat exchanger.
Keys take away: Thermophysical properties vary with pressure and temperature.
3.Types of heat exchanger in car
According to the application of heat exchangers in different fields of automobiles, it can be divided into:car exhaust heat exchanger, car fuel heat exchanger, car ac heat exchanger,car battery cooling heat exchanger, battery heating heat exchanger.
3.1 Car exhaust heat exchanger
Including EGR cooler, air charger air cooler, water charger air cooler, oil cooler and exhaust heat recovery system cooler(EGRS).
3.2 Car ac heat exchanger
Including condenser, evaporators & heater core. Condenser is dividing into air condenser and water condenser, some OEMs like BMW car is equip with water condenser with more stable performance compare with air condenser.
3.3 Car battery cooling heat exchanger
The battery cooling plate is mainly divided into extruded tube cooler, stamping plate cooler and rolling plate cooler according to the layout of the battery pack and the type of cell.
Keys take away: Competitive prices and lower mold opening costs for extruded tube batter cooler, while stamping plate cooler provide more cooling performance and small temperature difference.
3.4 Battery heating heat exchanger
The battery heating device is mainly divided into liquid heat and heating film. The main reason is that when the ambient temperature is relatively low, the battery charge and discharge rate is relatively small, especially when the low temperature fast charge is used, in order to meet the larger fast charge rate, the battery needs to be heated.
The heating film is divided into PI, PET and silicone heating film, etc., which are directly attached to the surface of the battery for heating, and the heating rate is fast, generally reaching a heating rate of more than 0.8°C/min. The heating film is a direct heating device, and the design needs to consider the area power, fuses, relays and temperature sensing devices.
Keys take away: Compared with battery water-cooled plate, the heating film provide a faster heating rate, and the battery low temperature fast charging rate is higher.
4.How heat exchanger design
How to design a heat exchanger? Heat exchanger in car is important especially for EV battery cooler plate.
Heat exchanger design how much cooling fluid volume required? Take battery cooler design guideline for example.
4.1 Determine the heat dissipation power of the battery water cooling plate
The battery power output table is converted according to the operating conditions of the whole vehicle, and then the calorific value of the battery is calculated according to the DCIR, SOC-OCV and thermal conductivity of the battery cells.
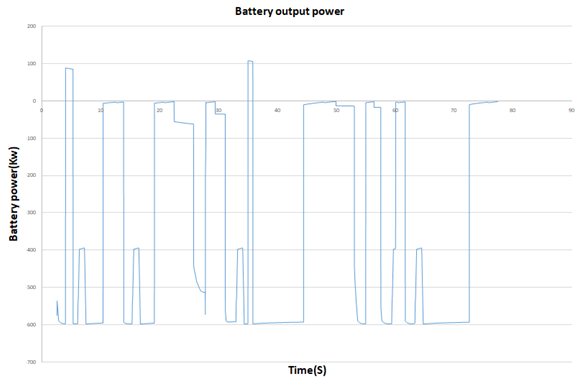
4.2 Analysis of factors affecting battery cooling plate
It is necessary to determine the heat conduction path, size and preliminary flow channel analysis of the water-cooling plate according to the arrangement of the entire battery pack module, the arrangement of the cells in the module, and the position of the liquid inlet and outlet of the entire battery pack.
4.3 Determine the cooling medium
Consider the following factors to determine the cooling medium: the heat dissipation power of the entire battery pack, the maximum temperature the battery is allowed to withstand, and the heat transfer coefficient of different cooling media. Such as using coolant(Ethylene Glycol) or refrigerant R1234yf or R134a.
4.4 Determine the cooling area
According to the corresponding coolant/refrigerant parameters, select the thermal interface material of the bottom of the cell and the battery cold plate, calculate the Z-direction thermal resistance, and calculate the heat exchange area.
4.5 Detailed Design battery cooling Plate
The detailed design of the battery cold plate is carried out in 3D modeling software. At the same time, it is necessary to consider temperature uniformity, burst pressure, strength, and manufacturing feasibility.
4.6 Simulation and optimization of battery water cooling plate
After the 3D modeling is completed, the flow field analysis and thermal analysis of the water-cooling plate can be performed, and the design of the water-cooling plate can be optimized.
Keys take away: A good battery water-cooling plate design requires several rounds of optimization.
If you need consulting design services, please contact us.