At the end of July 2023, under the high temperature of 48℃ in Turpan, BYD performed mediocrely. In terms of battery life achievement rate, only the Han EV 2023 Champion Edition is on the list in the top ten, and the achievement rate is only 70.7%, ranking at the bottom of the 10th place. Other pure electric models, including BYD Seal, Seagull, Yuan Plus, etc., have achievement rates ranging from 56.2% to 64%, and they are all out of the top ten. The results of high-temperature charging are the same. Except for Seal, which is barely the only lithium iron phosphate model in the top ten, the rest of the charging power is relatively poor. This result is very different from the results of the winter test in 2022. At that time, BYD Blade Battery’s model results were very impressive: three models were shortlisted for the top ten in terms of battery life, four models were shortlisted for low-temperature charging time, and the battery life of Han was 60 % first, Seal ranked first in 69 minutes of low-temperature charging. So the lithium iron phosphate system used in the blade battery theoretically has a worse low-temperature discharge retention rate. Why is it so far ahead in the winter test but mediocre in the summer test? How does this relate to the internal resistance of the blade battery? What role does the low-temperature self-heating technology that major car companies are currently proud of play in this? This article will take you through the analysis together.
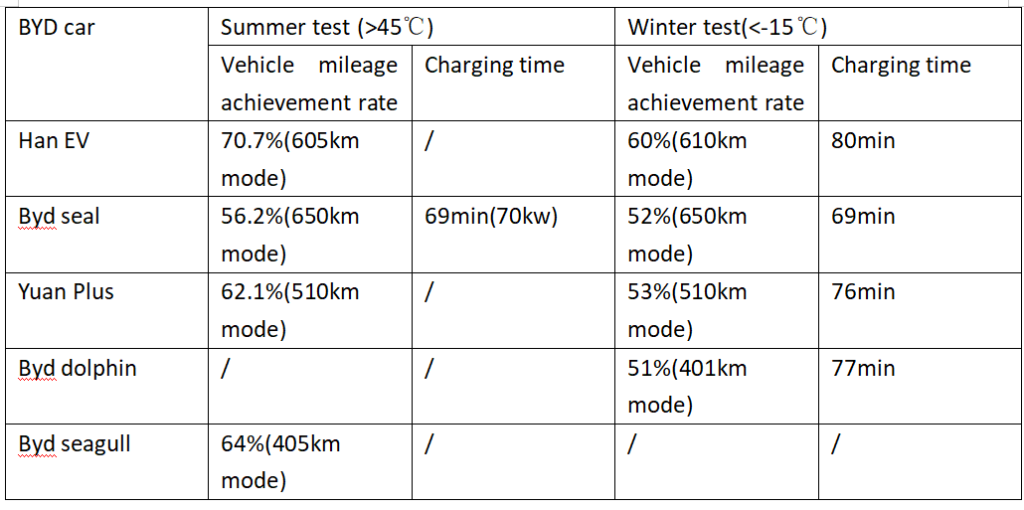
1.Battery low-temperature self-heating technology
Since the performance of lithium-ion batteries attenuates seriously at low temperatures, especially low-temperature battery life and low-temperature charging, the technology of heating batteries at low temperatures has always been an important research direction to promote the popularization of new energy vehicles. As early as 2016, Academician Wang Chaoyang, an expert in the field of thermal management, published an article in Nature. This structure embeds a thin nickel sheet with a certain resistance value into the interior of the battery, and uses the thin nickel sheet as a thermal element to heat the battery from the inside (the nickel sheet The thickness is adjustable from 5~200µm). The thin nickel sheet leads to two tabs, one of which is connected to the negative electrode of the battery, and the other tab leads to a separate pole, called the activation terminal (ACT). When the battery needs to be heated, the switch is closed and the active electrode is connected to the positive electrode. Current flows through the battery itself and the thin nickel sheet to generate heat to heat the battery. When the battery reaches the preset temperature, the switch is turned off, the thin nickel sheet is bypassed, and the battery works normally. The maximum heating speed exceeds 60℃/min (much greater than the 4℃/min of Changan and CATL). More importantly, , by increasing the number of nickel sheets to 3, the temperature difference inside the battery pole pieces can also be eliminated to a large extent, thus avoiding the inconsistency of SOC and rate during battery discharge, laying a good foundation for subsequent large-scale applications. Foundation. The resistance value shown by the author in the article is about 56mΩ. The size of the pole piece of the battery cell is about 15275mm. The reference resistivity of nickel is 6.8410-8Ω/cm. If the nickel sheet resistance is calculated according to R= ρL/3S , its thickness is indeed about tens of microns, and it also allows the space to be isolated and protected by non-conductive polymers on the surface.
Subsequently, his team relied on the concept of battery self-heating to create several battery systems: one is MFB = Maintenance Free Battery management-free battery. Its core concept is that battery energy and safety cannot have both. Through material surface coating and electrolyte The special design increases the internal resistance of the high-specific-energy battery, which is equivalent to passivating the battery, so that its safety will be improved. When needed, heating the battery can reduce the internal resistance and allow it to be used normally (you can refer to this idea for solid-state batteries). The other is the ACB=All Climate Battery all-climate battery, which can be used to heat the battery at low temperatures to improve discharge energy and overall efficiency. This will be used in vehicles with relevant technology at the 2022 Beijing Winter Olympics (with battery manufacturer Mengguli cooperate). Another one is FCB=Fast Charging Battery, which heats LFP or high-nickel ternary battery cells to 60°C for fast charging. Relevant articles have been published in Nature/Science and its sub-journals, with high impact factors and relatively large influence. However, according to the deputy director of the research institute of one of the top ten battery factories in the industry, this nickel-chip internal heating technology cannot be industrialized, and nickel chips can only be manually implanted to make batteries. Moreover, heating the battery core to a very high temperature will cause the worry of thermal runaway. The risk is currently not favored by mainstream car companies.
In addition to this self-heating technology, currently mainstream car companies mainly use battery pulse discharge for low-temperature heating. For example, Changan uses high-frequency alternating current to heat through lithium battery packs. The frequency is generally between 10Hz and 1kHz. 1kHz is the frequency range for testing the AC internal resistance of the battery. In this range, it is generally believed that no electrochemical reaction has occurred, which is harmful to the battery. Core performance is not affected. However, the internal resistance of high-frequency charging and discharging batteries is small, and the heating effect is poor; theoretically, the lower the frequency, the greater the internal resistance of the battery core, and the better the heating effect. However, pulse charging at low frequency is prone to side effects such as material particle fragmentation and lithium precipitation, so it cannot be too low. The micro-core high-frequency pulse heating technology adopted by Changan Deep Blue SL03 takes advantage of the characteristics of lithium-ion batteries that the internal resistance of the battery will increase at low temperatures. High-frequency positive and negative switching of large currents will not cause lithium deposition and will not affect battery safety and life. By controlling high-frequency pulses by switching on and off the IGBT driven by random variable frequency electricity, a large current and Joule heat of rapid positive and negative switching are generated, thereby achieving the purpose of rapid and even “self-heating” of the battery. When the vehicle is in an environment of -30°C, the battery pack can heat up by 4°C per minute at the fastest. In winter testing, the low-temperature charging performance of this model (515 pure electric version) was relatively good, with a completion time of 69 minutes, ranking second only to BYD Seal. As early as 2018, Ningde Times also applied for a related patent. By adding a device that can generate oscillating current at both ends of the battery, a large amount of heat is generated inside the battery to heat the battery. This technology has the advantages of high heating efficiency and uniform heating. It can heat all batteries simultaneously and increase the battery temperature by 4°C per minute. This technology is similar to Changan Deep Blue’s technology.
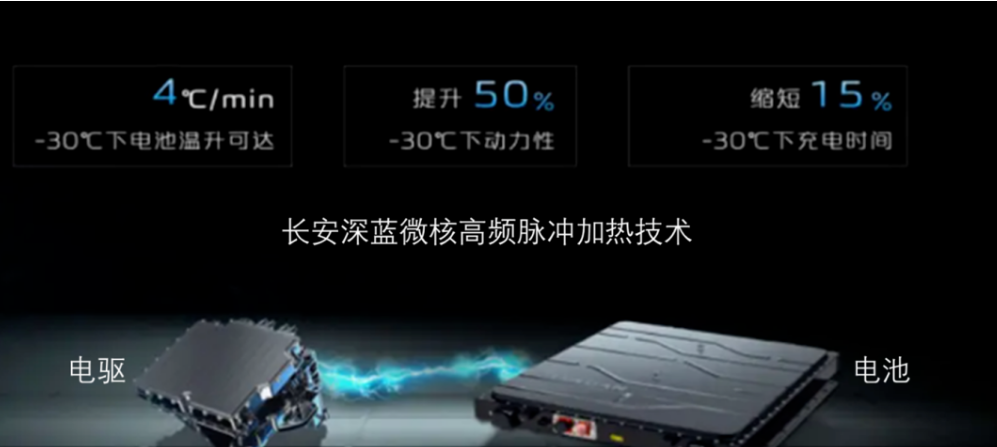
Changan SL03 Self-heating
2.Low temperature performance of blade battery
Although BYD only displayed one type of blade battery at the 2020 press conference, the length, width and height used in EVs were 96013.590mm respectively. However, in the field of hybrid power, the blade batteries used by BYD are in a different situation, using an internal series connection method, so the low-temperature self-heating technology of the two blade batteries is different.
The internal resistance of its current collector is indeed relatively large. The resistance of a single aluminum foil is 6.71mΩ, while the resistance of a single copper foil is 7.98mΩ. Since the entire battery core is composed of 26 positive electrode sheets, it is equivalent to 26 parallels, so the total current collector resistance is (6.71+7.98)/26=0.57 mΩ. And if the LFP battery cell of the same capacity is used with the aluminum shell battery cell with the same terminal lug from CATL, the total current collector resistance is less than 0.04 mΩ, which is almost negligible. Previously, the mainstream view was that such a large current collector resistor would have a negative impact on the performance of the battery cell, so such a long pole piece was usually not used. If it is changed to the L600 short knife battery of Honeycomb, Guoxuan and AVIC, the current collector resistor Can be reduced to about 1/4 of a long blade. However, at low temperatures, this understanding may be reversed, because heating the battery at low temperatures is a core need. Previously, Mr. Wang Chaoyang used the built-in nickel plate heating method, which requires adding about 3 nickel plates to more than 30 pieces of current collectors. BYD’s blade battery is equivalent to each pole piece acting as a resistor for heating. For the early Han EV The 138Ah battery cell used has 26 positive and negative electrode plates that can generate heat at the same time. The heating effect is naturally much better than other conventional battery cells. Especially in the case of continuous discharge or continuous charging, the accumulated heat is considerable. Let’s take charging as an example. The average charging power of BYD Seal in the winter test is close to 70kW, calculated based on 3.2V, 150Ah, 172 strings and -15℃ battery internal resistance of 1.5mΩ (assuming the number of positive electrode layers is still 26, and the total resistance of other electrical components Or 5mΩ), the required charging current is about 120A, the current collector heating power of a single blade battery is P=I2R=8.21W, and the total heating power of 172 strings is 1.4kW, which will heat the copper and aluminum foil of the battery core. Considering that the specific heat capacity of copper and aluminum foil is relatively small (copper 390 aluminum 880 unit J/kg.℃), and its mass proportion in the battery core is low, the temperature rise generated is relatively obvious (maybe close to 4℃/min) , the temperature of the positive and negative active materials has also been significantly improved, so the low-temperature charging time is very fast and the average power is relatively high. A similar situation occurs in Tesla’s German version of Model Y. BYD’s blade battery can maintain a charging power of 170kW in the 20~50% SOC range (the total heating power of the collector is expected to exceed 3kW), charging from 11% It only takes 15 minutes to reach 71%. However, the LFP battery with smaller resistance in the Ningde era only continued to decline after it began to reach peak power. When the battery SOC reached about 50%, the charging power was only maintained at about 110kW. It can be seen that the heat-generating effect of the large internal resistance of the blade battery collector not only improves the low-temperature charging experience, but also increases the charging power and shortens the charging time for fast charging at room temperature, which actually reverses the poor low-temperature performance of LFP materials. The high volume utilization further enhances the competitiveness of LFP batteries.
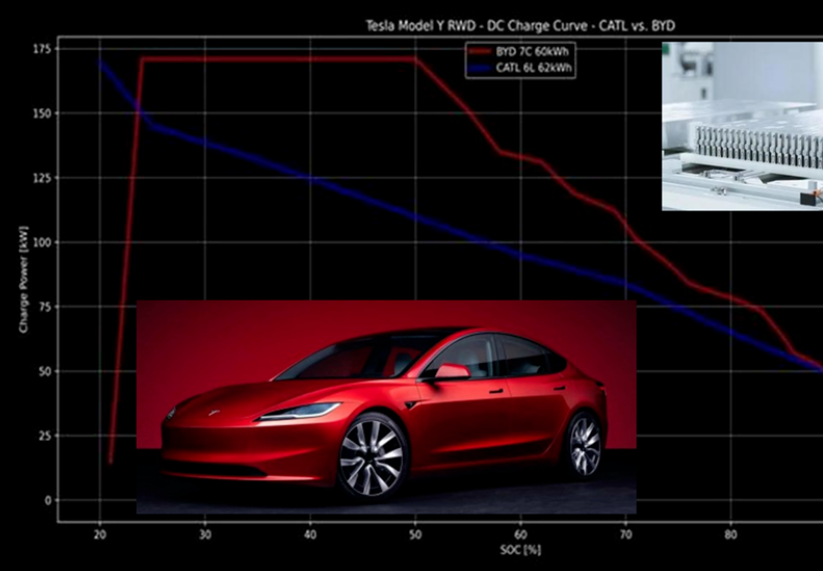
For the DM-i super hybrid dedicated power blade battery, the cells are connected in series. The internal resistance of a single cell is not large, especially the current collector resistance is relatively small and generates very little heat. BYD’s solution also uses high-frequency pulses to heat the battery core, but Changan uses AC pulses to control it through electric drives. In addition to similar control methods, BYD can also boost the voltage between two sets of lithium iron phosphate blade battery packs and discharge each other for heating. Since it is a DC discharge, the current will be relatively large and the heating effect will be relatively better. Therefore, BYD’s DM-i super hybrid model also performs quite well in winter.
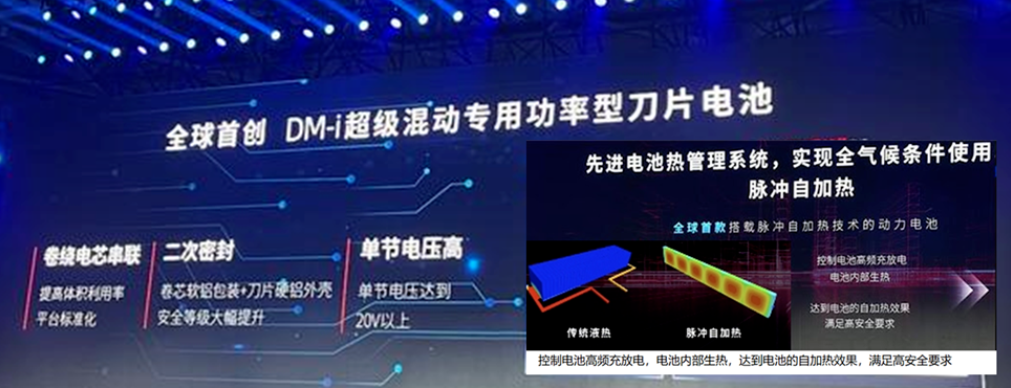
Overall, the low-temperature performance of blade batteries is better than that of ordinary lithium iron batteries. For EV pure electric models, this is mainly because its large current collector resistance brings a certain heating effect, similar to Wang Chaoyang’s built-in nickel plate heating. method, but the resistance is less than 1mΩ, which is much smaller than the 56mΩ of the nickel plate. But each pole piece can be heated, and its effect cannot be underestimated. And judging from the current actual measurement results, the battery life and charging performance of the blade battery at low temperatures far exceed expectations. However, although low-temperature performance is outstanding, high-temperature heating due to large resistance has become a problem, so the performance of BYD models in the summer test was surprising. But having said that, the hot weather above 45℃ in Turpan is an extreme working condition after all, and it is difficult for ordinary consumers to experience it.
3.Summary for car ev battery self-heating
Lithium iron phosphate batteries are intrinsically safe and have a long cycle life. The main bottlenecks restricting their large-scale application are low energy density, which leads to insufficient battery life, and poor low-temperature performance, which makes battery life even worse in winter. The emergence of the blade battery cleverly solved these two bottlenecks: first, the increase in volume group efficiency increases the vehicle’s charge, meeting the need for long battery life; second, the internal resistance of the battery cell is large and the temperature rises during low-temperature discharge. Obviously, it is equivalent to integrating self-heating technology, which significantly improves low-temperature battery life. It can be said that the blade battery reverses the inherent defects of lithium iron phosphate materials and expands the temperature scenarios for its application, which is indispensable for the increase in the market share of lithium iron batteries in the field of new energy vehicles in the past two years. Although such a design will lead to poor battery life and charging performance at high temperatures, after all, the application scenarios for extreme high temperatures are limited, and the battery has high activity at high temperatures, so it is not a bottleneck for most users. For ternary batteries, low temperature and battery life are not big bottlenecks. If it is made into a blade battery form, BYD feedback needs to invest more research in terms of collision (especially extrusion). In other words, the extrusion of a single battery cell may not pass, and the extrusion and vehicle collision after being made into a battery pack may not pass, because the intrinsic safety of ternary materials is too poor. Therefore, there will still be no ternary blade batteries in the short term, unless solid-state batteries can make a major breakthrough.
Therefore, currently battery pack integration still requires a battery cooling plate. If you need to customize and design a battery cooling plate, please contact us at [email protected]
Pingback: BYD's new DENZA N7 LFP battery technology news - vehiclethermal.com